参考3
製油所の脱硫装置における火災対策のポイント
*データ提供:危険物保安技術協会危険物等事故防止技術センター
1.製油所の脱硫装置における火災の全般的な傾向 |
    |
国内に設置されている石油脱硫装置のうち、直接重油脱硫装置およびその他脱硫装置(重油間接脱硫装置、重質油分解装置、灯軽油脱硫装置およびナフサ脱硫装置とし、接触改質装置のように脱硫工程を有していても装置の主目的が脱硫とは異なる装置は含まないものとした)に区分し、過去(1980年~2001年)の火災・爆発および漏洩事故を対象として調査分析を行った(1999.4.1現在、重油直接脱硫装置施設数16施設、その他脱硫装置施設数181施設)。 |
1.1 発生件数と発生率 |
    |
火災・爆発および漏洩事故を合わせた発生件数は、図1に示したとおり、直接重油脱硫装置で16件、その他の脱硫装置で22件、合計38件であった。対象装置は、ほとんどが危険物製造所として許可されていることから、危険物施設1万施設あたりの事故の発生件数(事故発生率)で表す。図2に示したとおり、危険物製造所における火災・爆発と漏洩事故を合わせた最近5年間の平均発生率は70.4件である。これに対して直接重油脱硫装置で750件、その他の脱硫装置で77.3件であった。従って、これらは、危険物施設の区分の中で事故発生率の最も高い危険物製造所区分のそれぞれ10.7倍および1.1倍で直接重油脱硫装置の危険性が際立って高いことが判る。
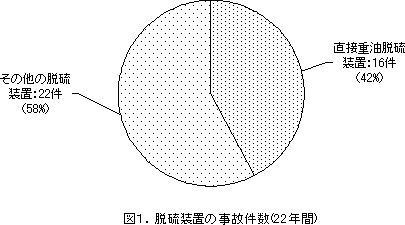
|
1.2 事故の発見の方法 |
|
それぞれの事故はどのような方法によって発見されたかについて、図3に示した。計器室での監視により発見されたのは18%となっているのに対し、巡回中、作業中および通りかかりの発見は56%と高い割合を示した。
|
1.3 事故時の操業状態 |
|
事故時の脱硫装置の操業状態を見ると、直接重油脱硫装置では定修中1件、定常運転中11件、シャットダウン中2件、スタートアップ中2件の計16件、その他の脱硫装置では定常運転中16件、シャットダウン中1件、スタートアップ中5件の計22件であった。脱硫装置全体を合算すると、定修中1件、定常運転中27件、シャットダウン中3件、スタートアップ中7件の計38件で、図4に示したとおり、全体の約71%が定常運転中の事故であった。
|
1.4 工程区分 |
|
事故の発生個所を工程別(定修中の事故事例1件は除外)に見ると、直接重油脱硫装置では反応工程における事故は9件、精製工程では6件の計15件、その他の脱硫装置では反応工程における事故は17件、精製工程では5件の計22件で、脱硫装置全体を合算すると反応工程における事故は26件、精製工程では11件の合計37件で、図5に示すとおり、全体の約70.3%が反応工程における事故であった。死者を伴うまたは損害見積額1,000万円以上の大きな事故についても、直接重油脱硫装置では4件(反応工程3件、精製工程1件)、その他脱硫装置では5件(反応工程5件)で、大きな事故の約88.9%が反応工程で起きていた。以上のことは、反応工程の危険度(リスク)が、精製工程のそれに比べ、極めて高い結果を示している。
運転条件について、内部流体から見ると、直接重油脱硫装置およびその他脱硫装置とも、反応工程では、原料油(直接重油脱硫装置では重質軽油(重油)、その他の脱硫装置ではナフサ、灯軽油、重質軽油(重油))、水素、反応により生成される脱硫重油、メタン、エタン等の軽質炭化水素、ナフサ、灯軽油、硫化水素および未反応水素が流れているのに対し、精製工程では、主として前者から硫化水素および未反応水素を除いた流体となる。このことから、腐食に対しては反応工程のほうが過酷な条件となる。反応工程は、精製工程に比較して、温度および圧力の面でも過酷な条件下で運転されている。従って、反応行程は、精製工程に比べて潜在危険性が一般的に高いと考えられる。
|
2.事故原因とその対策
2.1 発災部位および事故事象の区分 |
|
発災部位および事故事象に着目して、事故(定修中の事故事例1件は除外)の内容を検討すると、ある特定の部位または特定の事故事象に集中して事故が起こっていた。それらを以下のとおりに区分することができた。
(1) |
継手部に隙間が発生したもの11件(配管継手6件、熱交継手4件、弁継手1件)、 |
(2) |
主として水素、硫化水素による腐食、脆化等により配管、チューブ、弁等が開口したもの8件(行き止り配管3件、空気冷却器のチューブ1件、配管1件、弁1件、圧縮機付属緩衝器1件、塔1件)、 |
(3) |
ポンプのメカニカルシールに隙間が発生したもの6件、 |
(4) |
作業ミスによりスタートアップ時、弁を閉め忘れ、完全に閉めなかったまたはフランジボルトを弛めたため漏洩したもの3件、 |
(5) |
安全弁吹き出し時のチャタリングによる振動、運転時の振動により附属配管が破断または弁およびキャップが弛み漏洩したもの2件、 |
(6) |
塔の液面指示調節計取付け配管またはナフサ移送配管が経年腐食(主として水素、硫化水素による腐食、脆化等を除く)、劣化により開口したもの2件、 |
(7) |
その他、次のものが各1件であった。
・ |
加熱炉内加熱管が局所的に過熱され開口した。 |
・ |
流量計故障で窒素ガス流量不足のため、水素がタンク室に侵入し圧縮機が爆発した。 |
・ |
工事のさいの施工不良等により塔マンホール部に亀裂が発生した。 |
・ |
締め切り配管内の油が運転開始により昇温、昇圧したため、配管が内圧に耐え切れず亀裂した。 |
・ |
水注入(インジェクション)配管部が摩食、腐食により開口した。 |
|
以上の区分による割合を図6に示した。また、図7および図8には、それぞれ直接重油脱硫装置およびその他の脱硫装置に関して区分を(1)、(2)、(3)および(4)以降をその他にまとめて、発災の位置を示した。
特定の部位および特定の事故事象つまり(1)から(3)が全体に占める割合は68%と大きく、しかもこれらは反応工程側に集中している傾向が見られた。
|
|
2.2 事故原因および対策 |
|
発災の部位または事故事象の区分ごとに個々の事故例に関して原因およびその対策の要点を表1に記した。表1に示した対策はそれぞれの事故個々への対応策であり、発災部位および事故事象ごとにどのような原因で事故が発生し、それぞれへの対策が判る。発災部位ごとおよび事故事象ごとの今後の予防対策としてはそれらをまとめて総括的な対応を図る必要がある。ここで、発災の部位および事故事象区分(1)、(2)、(3)および(4)以降に関してそれぞれの対策をまとめると次の通りである。
(1) |
継手(配管継手、熱交換器継手、弁継手)部の漏洩防止対策
継手部の事故11件は全て反応工程で発生し、その内の10件は加熱炉出側から反応塔から熱交換器に至るまでの間の配管および熱交換器継手部で発生している。この部分は工程上最も温度、圧力の高い流体の存在する継手部に該当するところである。残る1件は原料油受け入れラインのフィルター切替弁継手部で発生している。
具体的な対策事項としては、設計、施工基準として運転温度、圧力および内部流体に応じた、配管・機器等の材質、フランジフェイスの材質および形状、ガスケットの材料および形状、ボルトの材質、締付冶具の指定、締付強さおよび方法(片締めを防止し、均一に配慮)、レインカバーの施工要領等がある。管理基準として昇温時、降温時の増し締め間隔(特にフランジ材質と異材ボルト使用時の増し締め間隔)設定、トルク管理の方法、フランジ部の開放・復旧作業の方法、点検の方法、頻度、適正な交換または修理に関する基準の規定化があり、それらの遵守が重要である。 |
(2) |
水素、硫化水素に原因した腐食、脆化による開口防止対策
腐食、脆化等による開口事故は、反応工程では7件、加熱炉出側から反応塔、熱交換器、高圧分離槽、吸収塔を経て補給水素ガス圧縮機付属緩衝器に至るまでの間の反応系およびガス回収系ラインの行き止り配管、集合配管、空気冷却器チューブ本体、弁本体、水素ガス圧縮器付属緩衝器本体で発生している。精製工程では1件、塔頂部で発生している。これらの部位は何れも腐食等の原因物質となる水素、硫化水素の循環ラインに該当するところから重点的に対策を検討する必要がある。
具体的な対策事項としては、設計、施工基準として塔、槽類等の機器および小口径配管を含めた配管について、運転温度、圧力および内部流体に応じて、使用材質の指定(炭素鋼使用の部分は、腐食環境中での余寿命を予測し、破壊に到る前に修理、交換等が実行される必要がある)、溶接施工要領の作成、点検を容易に実施するための架台の設置基準等がある。管理基準として、点検責任者の指定、点検部位、点検方法、点検頻度、使用機器、点検者の技術力の確保等を規定化し、励行する必要がある。
|
(3) |
ポンプメカニカルシール部の漏洩防止対策
メカニカルシール部の事故は、反応工程で4件、精製工程で2件発生している。設計、施工基準および管理基準を吟味する必要がある。
具体的要点として次のような事項がある。ポンプ出口逆止弁の点検頻度を適正にし、遠隔操作システムを設ける。モーター軸受部の温度および振動について遠隔監視システムを設ける。スラッジ堆積防止、サイクロンセパレーターの最適効率を維持するための措置を講じ、メカニカルシール漏洩防止を図る。リテーナー材質の不燃化、グリース管理、モーターの日常チェック体制を強化する。組み立てチェックシートを作成し、組み立て時の管理を徹底する。 |
(4) |
その他の安全対策
・ |
作業ミスに対して、確認表等による安全確認を徹底する。作業管理を徹底する。 |
・ |
振動または弛みに対して、ポンプの圧力を下げるためインペラーをカットし、圧力調整弁が全閉にならない機構を取付け、配管系のサポート補強を実施する。ドレン等の端末はすべて閉止フランジとする。支持具を強化する。 |
・ |
腐食、劣化に対して、オンサイト内での工事は運転を停止し可燃物の完全除去を確認後実施する。非破壊検査方法の充実を図り、点検頻度を規定化する。 |
|
以上の事故原因に対する個々の具体的対策に関して、さらにまとめると、次のようになる。潜在危険性の高い装置であることを認識して、設計・施工基準および保全管理基準の見直しを行い、その上でそれらの厳格な遵守を励行することである。また、ホットボルティングの技術管理およびポンプメカニカルシール対策に関しては、経験と勘による熟練技能を生かした合理的施工を実施する必要がある。 |
|
|
|